Optical fibre
hydrophone
System description
| Performance | Applications
| References | Contact
Ultrasonic hydrophones based upon piezoelectric PVDF sensing elements are widely used for
characterising medical and industrial ultrasound fields. However, a fundamental difficulty
arises in obtaining adequate detection sensitivity with the small (<100µm) element sizes
required for an omnidirectional response at MHz frequencies. Additionally, the sensitivity of piezoelectric hydrophones to EMI can present difficulties in the measurement of CW fields and their fragility and expense can preclude their use for the measurement of potentially damaging high amplitude fields and in hostile environments. With a view to overcoming these limitations, a prototype optical fibre hydrophone system, based upon the use of a Fabry Perot polymer film sensing interferometer
[4,5] has been developed in collaboration with Precision Acoustics Ltd. under the
EPSRC/DTI LINK Photonics programme. Applications include the assessment of the output of diagnostic and therapeutic medical ultrasound equipment, measurements of in vivo ultrasound exposure and characterisation of sources used in non destructive testing apparatus and ultrasonic industrial processes.
Back to top
System
description
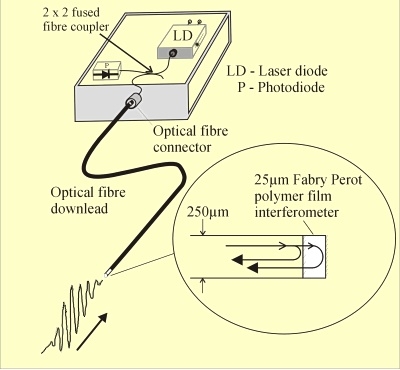
Figure 1
Schematic and photograph of the fibre optic hydrophone system.
The system, shown in figures 1 and 2, comprises an optics unit containing a tuneable DBR laser diode source, coupling optics and detection optoelectronics.
The output of the laser is launched via a 2x2 fibre optic coupler into a connectorised single mode optical fibre sensor downlead. The acoustically sensitive element comprises a 25μm thick Parylene film that is vacuum deposited
[4] on to the tip of the fibre and acts as a Fabry Perot interferometer - the mirrors of which are formed by the deposition of optically reflective coatings. An incident acoustic wave modulates the thickness of the film and hence the optical phase difference between the light reflected from the two sides of the film. This produces a corresponding reflected intensity modulation which is then transmitted back along the fibre to the optics unit where it is directed, via the fibre coupler, to the photodiode. To set the phase bias of the interferometer to the optimum working point, the laser wavelength is thermally tuned by adjusting the temperature of the laser diode (for more on the transduction mechanisms
[3], click here).
The advantages of this approach over piezoelectric based methods are:
- Small effective radius - The
use of a single mode fibre (core diameter <10µm) to illuminate the
sensing film enables acoustically small element sizes to be achieved.
These are required for an omnidirectional response and to avoid errors
due to spatial averaging. Unlike piezoelectric detection, this does
not come at the expense of detection sensitivity as element size and
sensitivity are independent.
- Inexpensive fabrication - Fabrication of the interferometer using vacuum deposition methods
enables a rugged sensor head to be batch fabricated with good
repeatability at low unit cost for single use applications.
- Self – calibration - Modulating
the phase bias and detecting the corresponding output of the
interferometer enables changes in sensitivity to be continuously
monitored.
- Simultaneous temperature and
pressure measurement
- Thermally induced changes in the optical thickness of the
interferometer enable temperature changes to be measured for
investigating effects such as ultrasound induced heating.
- Electrical passivity and immunity to EMI - Measurements of
cw fields and measurements in electrically noisy environments can be
made without the "breakthrough" experienced with
piezoelectric detectors.
Back to top
Performance
Sensitivity
| Linearity | Frequency response
| Directivity | Stability
| Temperature sensitivity
The system as been carefully
characterised and compared to the performance of PVDF needle and membrane hydrophones
[4]. A summary of performance is provided in the
table below. Click on the relevant links in the table for more detailed
characteristics and intercomparisons with PVDF devices.
Back to top
Applications
In addition to
general field measurement and characterisation, a specific application
is the in situ measurement of ultrasound exposure produced by
diagnostic and therapeutic medical ultrasound equipment. For this, the
disposable nature of the hydrophone, its miniature, flexible probe-type
configuration, low directional sensitivity, electrical passivity and
ability to measure temperature are of particular benefit. Another single
use application is the measurement of high amplitude fields such as
those produced by shockwave sources (e.g. lithotripters) or detection in
hostile environments (e.g. corrosive liquids) where there is a risk of
damaging expensive PVDF hydrophones. Additionally, the system is suited
to the measurement and monitoring of cw low frequency high power
industrial ultrasound such as that employed in ultrasonic cleaning which
requires small physical size to avoid disturbing standing wave patterns,
the ability to withstand hostile environments and low sensitivity to
electrical interference. The concept may also be suited to detection
applications such as acoustic emission studies, transmission ultrasound
imaging, photoacoustic and Hall effect imaging all of which require a
small aperture wideband receiver.
Back to top
|